Well sad to report that our order for SRAM E-Tap was cancelled by the supplier because SRAM pushed out the shipping date. As such we lost our spot in the queue. So while I search for another source I thought we would do an update with some parts we do have.
So today we are going to make Frogs Float.
When picking a Clipless pedal for your Vendetta it's important to pick a pedal that matches your body needs and your goals. For a lot of people (not everyone) these goals include
Easy Clip in
Easy Clip out
A walkable Shoe
Certainty of unclipping when falling
Lots of "float" to protect the knees
Affordable
Ticking all those boxes is the venerable "Frog" pedals from Speedplay. The Cromoly version of these can be had for around $105US and the Stainless ones for $135. You really should not use the Titanium ones on a Recumbent bike because they have a weight limit and you could easily exceed that amount of force if you brace into the seat and push hard.
The Cromoly option, has a black painted spindle that might chip over the course of time and you should be prepared to touch them up with paint to prevent rust; otherwise they are functionally equivalent to the Stainless option and about a 5g delta in weight.
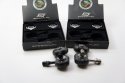
Frogs have been around a long time. They are a mountain bike pedal with a 2 hole cleat. As such they work with all walkable MTB two hole shoes.
The cleat and pedal are completely spring-less; making them pretty much the easiest pedal on the mark to "click into". With the frogs you simple place your foot up by the pedal and click you are attached. If you have ridden other clip-less pedals it is rather shocking how easy it is. This is my personal favorite pedal for teaching people to ride clip-less on.
To unclip from Frogs you simply rotate your heel out past 15 degree and the shoe literally falls off the pedals. Oddly this disengagement is not something that happens accidentally; they float so freely that at time you will think that would happen, but in practice it just does not happen.
As designed the Frog pedal only disengages with a heel "out" rotation; there is a physical stop on them that lets you squeeze your heels inward that ensures you stay locked in. This feature was meant to allow MTB riders to got air born while squeezing there heels to ensure the bike stays attached to the feet. The rotation stop also ensures you heel does not come into contact with the crank arms or the chain stay. These are both good design elements and they can be used as is with a Cruzbike or other recumbent. However, for riders with bad knees that lack of inward float of about 1-5 degree can be frustrating and can aggravate finicky knees. If you are a rider with knees that need more float you are in luck because the frogs can be modified to be the best free floating casual pedal available. So lets take a look at this modification. If you don't like the modification it's trivial to undo it.
To setup the Floating frogs and shoes you need; Pedals, a Grease gun, a thin knife, and a 2.5nm torque wrench. You might be thinking, I'd don't want to buy a Pedal grease gun, but really if you do not have one your pedals are probably letting you down as most pedal designs should be greased at least once a season probably twice; and it really is trivially cheap and easy to do.
Using 4mm allen remove the two screws from the left and right of the pedal body.
Insert a thing knife into the tiny notch on the back edge of the pedal. The bodies are designed to come apart for maintenance and replacement. Look closely and you will see the notch for separating the halves.
Pry the body apart.
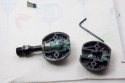
Remove the spindle. This might be a touch hard; the factory pedals have some glue to hold the halves together and some always seems to get on the spindle making it hard to remove. There are no plastic pieces holding it in place; just give it a firm tug and it will come out; there is nothing to break.
Repeat the process with the second pedal. Then with both pedals apart; simply SWAP the spindle. Pair the Left spindle with the right pedal, and the right spindle with the left body; and reassemble. You now have two pedals with full float.
The last step for the pedals is to re-grease them. Remove the screw from the end of the pedal.
Insert grease gun
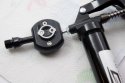
Squeeze in grease until some comes out the spindle side of the pedal.
Comparing a modified and unmodified pedal you can see that the rotation stop is now at the front of the pedal and will never actually engage with the cleat, thus giving you a full float pedal.
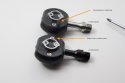